Welcome to the world of Parker Hydraulic Motors, where we delve into the inner workings, mechanisms, and operational principles of these remarkable devices. In this guide, we aim to provide an in-depth analysis of Parker Hydraulic Motors and their importance in various applications. Hydraulic motors play a vital role in converting hydraulic energy into mechanical power, driving numerous machinery and systems. By understanding the intricacies of Parker Hydraulic Motors, you can unlock their potential for effective utilization and maintenance. Join us as we explore the fascinating world of Parker Hydraulic Motors and gain insights into their significance in various industries.
Understanding Parker Hydraulic Motors
Parker Hydraulic Motors have established themselves as a reputable brand in the industry, renowned for their high-quality hydraulic motor solutions. To truly understand the capabilities of Parker Hydraulic Motors, it’s essential to familiarize ourselves with their basic components, construction, and fundamental principles.
At the heart of every hydraulic motor lies a combination of essential components, including pistons, cylinders, and a rotary mechanism. These components work in harmony to convert hydraulic energy into mechanical power, allowing machinery to perform a wide range of tasks.
Parker Hydraulic Motors are designed with precision and expertise, ensuring optimal performance and longevity. They boast a range of features that set them apart, such as high torque output, precise control, and efficient power transmission. These motors come in various sizes, types, and variations to suit different applications and requirements.
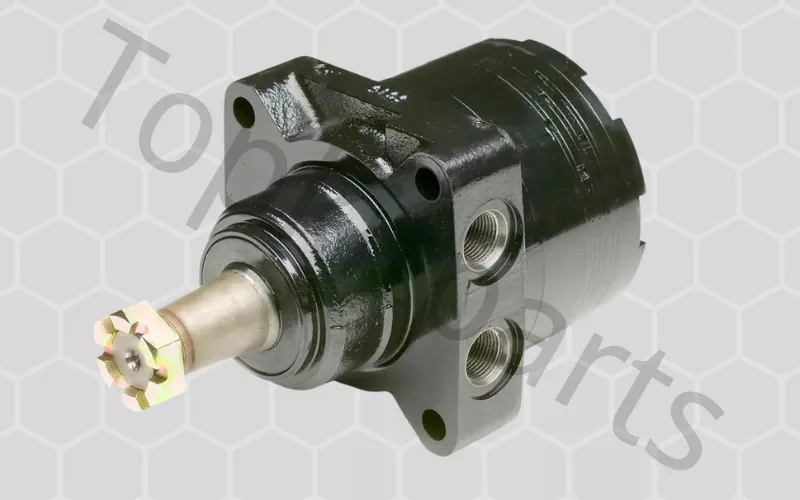
Understanding the fundamental principles of Parker Hydraulic Motors is crucial. These motors operate on the principles of fluid dynamics, utilizing the force of pressurized hydraulic fluid to create rotational motion. The flow of hydraulic fluid, along with pressure differentials and displacement, drives the movement of the motor, ultimately producing mechanical power.
Parker Hydraulic Motors are trusted for their reliability, durability, and versatility. They find applications in various industries, including construction, agriculture, manufacturing, and more. From powering heavy machinery to controlling precise movements, Parker Hydraulic Motors play a vital role in driving efficiency and productivity.
In the following sections, we will explore the inner workings, mechanisms, and operational principles of Parker Hydraulic Motors in greater detail. Stay tuned to gain a comprehensive understanding of these remarkable devices and their impact in the world of hydraulics.
Hydraulic Motor Mechanisms
To truly appreciate the functionality of Parker Hydraulic Motors, it’s essential to explore the mechanisms involved in their operation. These mechanisms bring together the power of hydraulic energy and the precision of mechanical motion. Let’s dive into the fascinating world of hydraulic motor mechanisms.
Parker Hydraulic Motors operate based on the principle of converting hydraulic energy into mechanical power. The key components involved in this conversion include pistons, cylinders, and a rotary motion mechanism.
When pressurized hydraulic fluid enters the motor, it exerts force on the pistons within the cylinders. The pistons move back and forth, driven by the hydraulic pressure. As the pistons reciprocate, they transfer their motion to a rotary mechanism, which translates the linear motion into rotational motion.
The rotary mechanism is responsible for converting the linear motion of the pistons into the desired rotary motion. This mechanism can take various forms, depending on the specific design of the hydraulic motor. Common examples include gears, vanes, or swash plates, each offering unique advantages and characteristics.
Regardless of the specific mechanism used, the goal is to transform the continuous flow of hydraulic fluid and the reciprocating motion of the pistons into a smooth and continuous rotational motion. This rotary motion is then utilized to drive various machinery and systems, enabling them to perform their intended tasks.
Parker Hydraulic Motors are designed with precision engineering and advanced technologies to optimize the efficiency and reliability of these mechanisms. Their robust construction, high-quality materials, and precise manufacturing techniques ensure smooth operation and longevity.
By understanding the mechanisms involved in Parker Hydraulic Motors, you gain insight into the intricate process that enables these motors to convert hydraulic energy into mechanical power. This knowledge forms the foundation for effectively utilizing and maintaining these motors in various applications.
In the next section, we will delve into the operational principles of Parker Hydraulic Motors, examining how fluid flow, pressure differentials, and displacement contribute to their performance. Stay tuned to uncover the fundamental principles that drive the efficiency and functionality of these remarkable hydraulic motors.
Operational Principles of Parker Hydraulic Motors
The operational principles of Parker Hydraulic Motors revolve around fluid flow, pressure differentials, and displacement. These principles govern the performance and efficiency of the motors, ensuring optimal operation in various applications. Let’s explore these operational principles in more detail.
- Fluid Flow: Parker Hydraulic Motors rely on the controlled flow of hydraulic fluid to generate mechanical power. As pressurized fluid enters the motor, it flows through channels or passages that direct the fluid to the appropriate areas. The flow of hydraulic fluid within the motor is carefully regulated to ensure smooth operation and efficient power transmission.
- Pressure Differentials: Pressure differentials play a crucial role in driving the movement of hydraulic motors. By controlling the pressure levels within the motor, the motor can generate the necessary force to perform work. The pressure differential between the inlet and outlet of the motor creates a driving force that propels the pistons and generates rotational motion.
- Displacement: Displacement refers to the volume of hydraulic fluid that is displaced or moved by the motor during each cycle. It is an important factor that influences the motor’s performance and torque output. The displacement capacity of a hydraulic motor determines the amount of mechanical power it can generate.
Parker Hydraulic Motors are designed to optimize these operational principles, ensuring efficient performance and power transmission. Factors such as the design of internal components, hydraulic fluid properties, and system configuration all contribute to the overall operational efficiency of the motors.
Hydraulic fluid and system design also play a vital role in optimizing the operation of Parker Hydraulic Motors. Choosing the appropriate hydraulic fluid with the right viscosity and properties ensures smooth flow and minimal friction within the motor. Additionally, a well-designed hydraulic system that takes into account pressure requirements, flow rates, and overall system compatibility contributes to the efficient operation of the motors.
Understanding the operational principles of Parker Hydraulic Motors provides valuable insights into their performance and functionality. By leveraging these principles, industries can harness the full potential of these motors to optimize their machinery and achieve enhanced efficiency.
In the next section, we will explore the different types and variations of Parker Hydraulic Motors, understanding their specific characteristics and applications. Join us as we uncover the diverse range of options available to meet various industry needs.
Types and Variations of Parker Hydraulic Motors
Parker Hydraulic Motors offer a diverse range of types and variations to suit different applications and industry requirements. Understanding these types and their specific characteristics is essential for selecting the most suitable motor for a particular task. Let’s explore the various types and variations of Parker Hydraulic Motors.
- Radial Piston Motors: Radial piston motors feature pistons arranged radially around a central shaft. They offer high torque output, making them ideal for applications requiring substantial power. These motors excel in heavy-duty operations such as construction equipment, mining machinery, and marine propulsion systems.
- Axial Piston Motors: Axial piston motors utilize pistons arranged in a circular pattern around a central shaft. They offer a compact design, high power density, and efficient operation. These motors are commonly used in mobile equipment, agricultural machinery, and industrial systems that require precise control and high torque.
- Gear Motors: Gear motors utilize interlocking gears to transfer power and produce rotational motion. They offer simplicity, cost-effectiveness, and reliability. Gear motors find applications in various industries, including material handling equipment, winches, and small-scale machinery.
Each type of Parker Hydraulic Motor has its own unique characteristics and advantages. They differ in terms of torque output, speed range, efficiency, and suitability for specific applications. By understanding the strengths and limitations of each type, industries can select the most appropriate motor to meet their operational requirements.
Furthermore, within each type, Parker Hydraulic Motors offer variations with different specifications, sizes, and performance capabilities. These variations allow for further customization and fine-tuning to match specific application needs. For example, variations may include different displacement options, speed ranges, and mounting configurations.
Parker Hydraulic Motors’ commitment to innovation and technological advancements ensures that their motor offerings stay at the forefront of hydraulic power solutions. They continue to develop new variations and improve existing designs to meet the evolving needs of industries across the globe.
In the next section, we will explore the factors that influence the efficiency and performance of Parker Hydraulic Motors. By understanding these factors, industries can optimize the utilization of these motors and achieve enhanced productivity. Join us as we dive into the considerations that impact motor efficiency and performance.
Efficiency and Performance Considerations
Efficiency and performance are crucial factors to consider when utilizing Parker Hydraulic Motors in various applications. Understanding the key factors that influence their efficiency and performance allows industries to optimize their utilization and achieve enhanced productivity. Let’s explore these considerations in detail.
- Volumetric Efficiency: Volumetric efficiency refers to the ability of a hydraulic motor to effectively convert hydraulic fluid flow into mechanical power. It is influenced by factors such as internal clearances, sealing efficiency, and overall design. Higher volumetric efficiency translates to improved motor performance and reduced energy loss.
- Mechanical Efficiency: Mechanical efficiency relates to the ability of a hydraulic motor to convert hydraulic energy into mechanical power with minimal losses due to friction and internal resistance. Factors such as bearing quality, internal sealing, and overall motor design impact mechanical efficiency. Higher mechanical efficiency results in improved power transmission and reduced energy wastage.
- Speed Control: The ability to control the speed of a hydraulic motor is crucial in achieving optimal performance in different applications. Parker Hydraulic Motors offer various speed control mechanisms, such as variable displacement, flow control, and pressure regulation. Effective speed control allows for precise operation, energy optimization, and improved overall efficiency.
- Design Features and Engineering Techniques: Parker Hydraulic Motors incorporate advanced design features and engineering techniques to enhance their efficiency and performance. These include optimized porting, improved sealing systems, reduced internal friction, and enhanced cooling mechanisms. These design features contribute to improved efficiency, reliability, and longevity of the motors.
Industries can optimize the efficiency and performance of Parker Hydraulic Motors by considering these factors. Selecting the appropriate motor with high volumetric and mechanical efficiency, coupled with effective speed control, ensures optimal power utilization and minimized energy losses.
Furthermore, proper installation, regular maintenance, and adherence to recommended operating conditions play a vital role in maximizing motor efficiency and performance. This includes maintaining proper fluid cleanliness, monitoring system pressure and temperature, and periodic inspection and servicing of the motor.
By considering these efficiency and performance considerations, industries can harness the full potential of Parker Hydraulic Motors, achieving enhanced productivity, energy optimization, and cost-effectiveness in their operations.
In the next section, we will delve into the maintenance and troubleshooting aspects of Parker Hydraulic Motors, providing valuable insights on how to ensure their optimal performance and reliability. Join us as we explore the key maintenance practices and troubleshooting techniques for these remarkable hydraulic motors.
Maintenance and Troubleshooting
Maintaining the optimal performance and reliability of Parker Hydraulic Motors is crucial to ensure their longevity and efficient operation. Proper maintenance practices and troubleshooting techniques play a vital role in identifying and resolving any issues that may arise. Let’s explore the key aspects of maintenance and troubleshooting for Parker Hydraulic Motors.

- Recommended Maintenance Practices: Following the manufacturer’s recommended maintenance practices is essential to keep Parker Hydraulic Motors in top condition. This includes regular inspections, cleaning, and lubrication as per the specified intervals. Routine maintenance tasks also involve checking for any leaks, monitoring fluid levels, and ensuring proper alignment and mounting.
- Common Issues and Troubleshooting: Despite their robust design, Parker Hydraulic Motors may occasionally experience issues. Understanding common issues and having troubleshooting techniques in place can help identify and resolve problems promptly. Common issues may include loss of power, overheating, excessive noise, or fluid leakage. Troubleshooting techniques involve diagnosing the root cause of the problem and taking appropriate measures, such as adjusting pressure settings, replacing worn-out seals, or cleaning clogged filters.
- Diagnostic Techniques: Diagnostic techniques are essential in identifying any underlying issues with Parker Hydraulic Motors. These techniques involve monitoring performance indicators such as temperature, pressure, and flow rates. Regular monitoring and data analysis help detect any abnormalities or deviations from normal operating conditions. Utilizing diagnostic tools such as pressure gauges, temperature sensors, and flow meters enables accurate assessment of motor performance.
- Preventive Maintenance: Implementing a preventive maintenance program is highly recommended to ensure the long-term reliability and efficiency of Parker Hydraulic Motors. This includes scheduled inspections, routine servicing, and timely replacement of wear parts. By proactively addressing potential issues, industries can minimize downtime, extend the motor’s lifespan, and optimize overall productivity.
Industries should also adhere to proper storage practices when hydraulic motors are not in use for an extended period. This involves protecting the motor from environmental elements, ensuring proper cleaning and lubrication, and storing in a secure and controlled environment.
By following these maintenance practices and troubleshooting techniques, industries can maximize the performance, reliability, and lifespan of Parker Hydraulic Motors. Regular maintenance not only prevents potential issues but also helps identify any underlying problems before they escalate, ensuring uninterrupted operation and optimal productivity.
In the concluding section, we will recap the inner workings, mechanisms, and operational principles of Parker Hydraulic Motors. We will reinforce their importance in various applications and encourage readers to gain a deeper understanding of these remarkable motors for effective utilization and maintenance.
Conclusion
Throughout this guide, we have explored the inner workings, mechanisms, and operational principles of Parker Hydraulic Motors. These motors play a vital role in enhancing machinery efficiency and powering various applications across industries. Let’s recap the key points discussed and reinforce their importance.
Parker Hydraulic Motors are renowned for their reliability, efficiency, and versatility. Understanding the basic components, construction, and fundamental principles of these motors allows industries to harness their full potential. From radial and axial piston motors to gear motors, Parker offers a diverse range of options to suit different applications and requirements.
Efficiency and performance considerations, such as volumetric efficiency, mechanical efficiency, and speed control, influence the overall effectiveness of Parker Hydraulic Motors. By selecting the most suitable motor and optimizing these factors, industries can achieve enhanced productivity and energy optimization.
Maintenance and troubleshooting are essential to ensure the optimal performance and longevity of Parker Hydraulic Motors. Adhering to recommended maintenance practices, promptly addressing common issues, and implementing a preventive maintenance program help maintain reliable operation and minimize downtime.
In conclusion, Parker Hydraulic Motors are key components in driving machinery efficiency, productivity, and cost-effectiveness. By gaining a deeper understanding of these motors and their operational principles, industries can effectively utilize and maintain them to optimize their applications.
We encourage you to continue exploring the world of Parker Hydraulic Motors, taking advantage of their capabilities and seeking further insights into their specific applications. By leveraging the power of these motors, you can unlock enhanced efficiency, reliability, and performance in your machinery and systems.
Thank you for joining us on this journey through the analysis of Parker Hydraulic Motors. Should you have any further questions or require assistance, please don’t hesitate to reach out.
Related Keywords
# Parker Gear Pump catalog,
# Parker Wheel Motor Rebuild Kit,
# Parker 4 Ton Winch Motor,
# Parker Pump and Motor Division Greeneville TN,
# Parker Pump catalogue,
# Commercial hydraulic pump cross reference,
# Parker Motors,
# Parker Wheel motor parts diagram,